The Minister for Defence Procurement and Industry, Maria Eagle, announced the new MaST agreement Monday, on a visit to Somers Forge yesterday, based in Halesowen. The new agreement gives small and medium sized companies the chance to bid for work under a seven-year framework, worth up to £850 million.
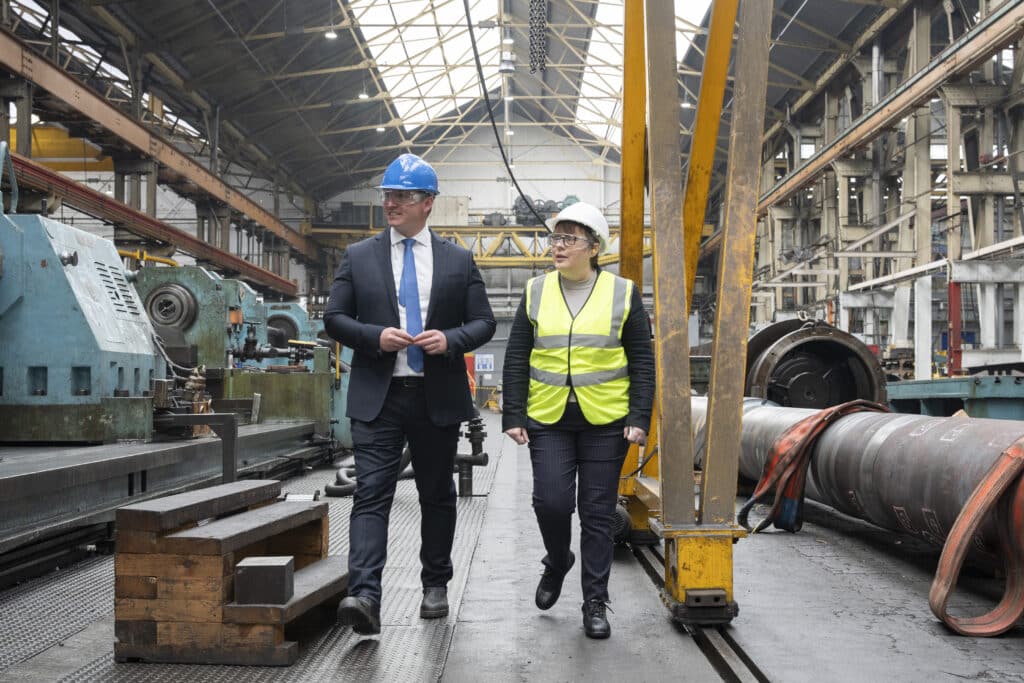
Our Thoughts
“As a multi-generational family business, it was an honour to host the MaST framework announcement at our Midlands-based forging and engineering company. Our workforce possesses extensive traditional and modern engineering skills which are essential to supporting the UK’s current and future sovereign capabilities. I feel the announced framework is a pertinent step towards ensuring that UK SME manufacturing companies, such as ours, continue to play an important role in MOD contracts well into the future”.
Amy Folkes, Group Director
During the site visit, MinDPI witnessed first-hand the advanced forging processes on the hammers and presses, including seeing a 36 tonne ingot being forged in our heavy forge. The event saw many key figures from the MOD, including Toni Gray, Programme Director, along with other top industry leaders such as Dr. Simon Dakin, Director Integrated Battlespace and Samira Braund, ADS Group Defence Director.
”Being selected for the MAST framework represents a huge opportunity for our business. We have been a defence supplier since 1912 and are incredibly proud of our heritage supporting the Royal Navy. For Somers Forge, winning contracts through MAST can help us sustain vital jobs and apprenticeships in the Midlands, as well as underpin our growth ambitions.”
Samson Folkes, Managing DirectorHosting this announcement is a significant milestone, especially since opportunities like this typically go to large primes. It underscores our unwavering commitment to bolstering the UK’s defence capabilities.
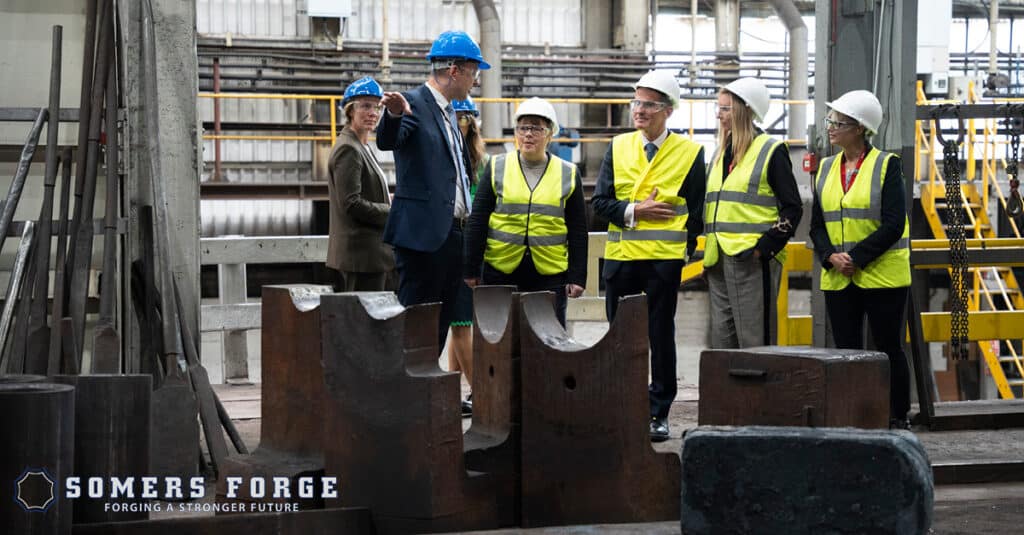